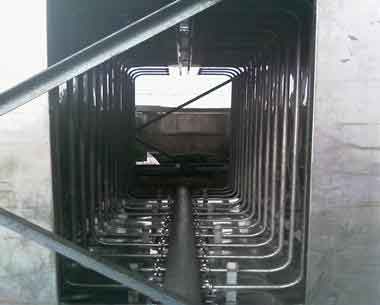
Pre Treatment Process
It can be a three tank to eleven tank process.
After pre treatment, water drying tank or water drying oven can be placed in line or off line. Processes are usually designed depending upon the requirement of final finishing process.
Eg. Seven tank process is usually preferred in automobile industry.
Pretreatment process can be made of spray type or dip type.
Depending upon the chemicals used system can be made cold or hot type.
Depending upon the type material handling is defined i.e. using conveyor, monorail & hoist, transporter.
Pretreatment tanks are manufactured in MS or SS 5 mm thk.
Dip type Pretreatment
The solutions offered by us are proposed only after detail study of the final requirement of the product, which enables us to have absolute clarity of the project in the beginning enabling us to deliver the final product within shortest possible time.
We have executed many projects on turnkey basis in record time for various applications in automobile industries, home appliances industries etc.
We request you to go through the enclosed product range and the various products and send us your valuable enquiry in order to give us an opportunity to have yet another satisfied customer to the list of our esteemed customers.
Spray type Pretreatment
Enclosure Material GI or SS304,Piping SS 304. Pressure aviable inside between 1-3 bar depending upon the requirement.